Rust formation on ferrous metal parts after machining and grinding operations is costly for companies. They either perform additional processes to re-work and de-rust the metal parts or they treat it as “reject”.
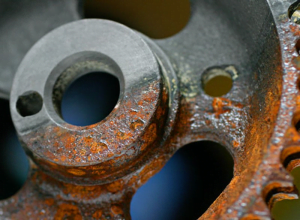
Rusting can be caused by a number of reasons, one being the improper use of water soluble coolants. To prevent rusting due to this, consider the following factors:
1. Coolant Concentration
One of the main reasons for rust formation is using coolant at low concentration. When too much water is used, the oil and anti-rust additives in the emulsion run low. Ideally, emulsions and semi-synthetics should be at >5% concentration. Refractometers can be used to easily check the coolant concentration.
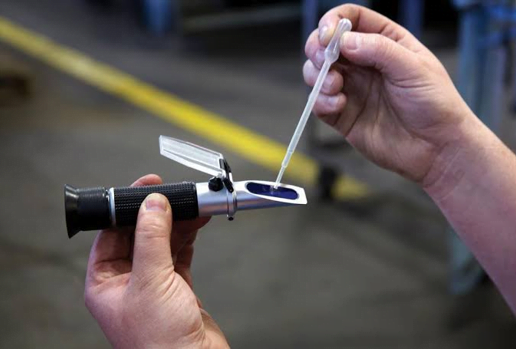
2. Bacterial Growth
Presence of bacteria in coolants is usually indicated by the foul smell which machine operators are familiar with. Anti-rust additives are consumed by these bacteria resulting in the rusting of machined parts. To avoid this, coolants should be maintained at right concentrations so that the biocides can take effect. pH should also be maintained and chips at the bottom of the sump should be removed where they usually thrive to discourage bacterial growth.
3. pH
To prevent growth of bacteria, coolants should be maintained at pH levels of 8.9 and above. pH meters are normally used to quickly monitor the pH of the coolant in the sump.
4. Excess Tramp Oil
When slideway oils and hydraulic oils leak into the coolant sump, rust formation can occur. Since these oils are already used and may have been oxidized, contaminated workpieces might not be protected against rust. Skimming the oil manually using a dipper or installing an automatic oil skimmer usually does the job.
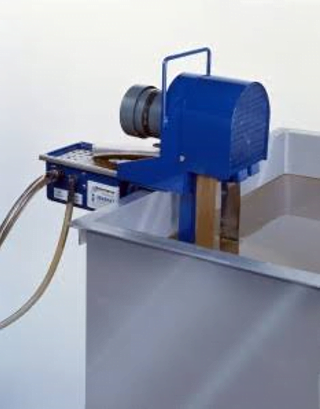
Acidic environment (machining close to acid pre-treatment processes), high humidity levels, prolonged storage after machining or grinding operations without applying rust-preventive fluids, and water with high dissolved solids are also contributing reasons to rusting.